
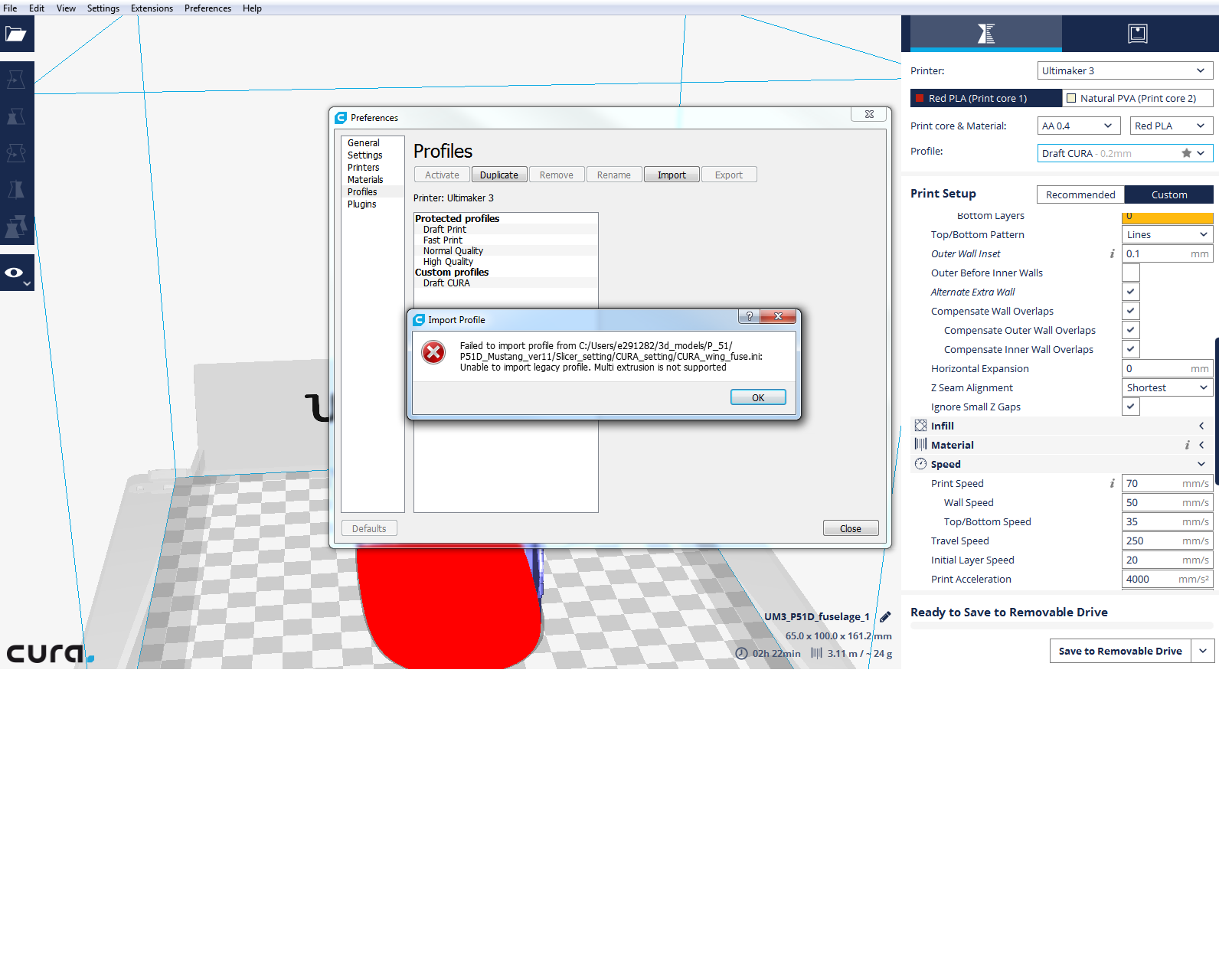
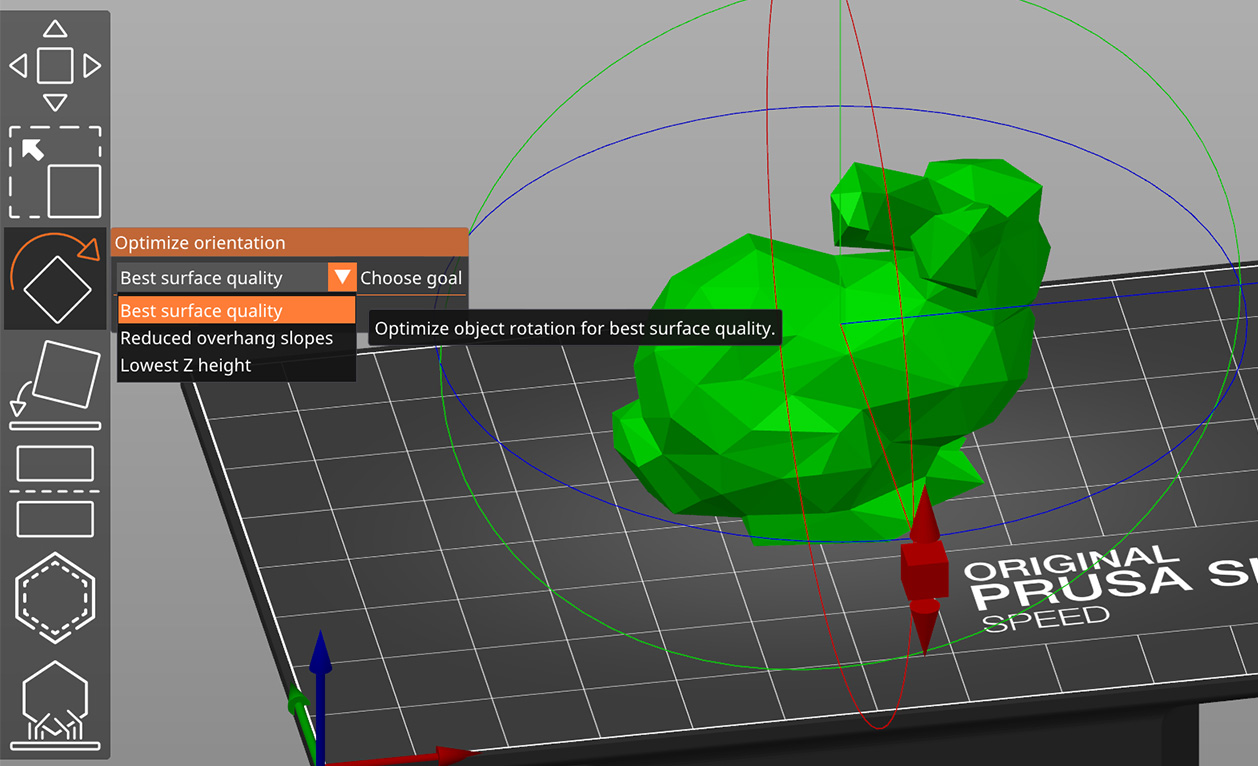
The following panel, beginning with the overlap is then placed over the underlap, concealing the fixing clips and the seam is mechanically closed with a seam closer available at our store. Panels are laid directly over the membrane and clips are used to fix the underlap with the accredited fasteners. All panels are to be laid on a solid substrate, which is then wrapped in a vapour barrier membrane. In other slicing software you could at least increase the width to 130-150 and reduce speed for the first layer. You can use separate process in Simplif圓D. Ventilation is recommended to remain at the top and bottom of all panels where possible. For better strenght of printed parts and better bed adhesion is vital setting 2 perimeters for the first 1-3 mm of print. 20mm for all facade and cladding projects and a 40mm continuous air gap for roofing installations. Standing Seam installations require a continuous ventilation gap beneath the plywood substrate. This system is widely used for it’s key attributes weather resistance to harsh climates and the ability to create watertight solutions, even in areas subject to coastal spray, snowfall, high winds and heavy rain. Standing Seam is a timeless style profile, with its classic longitudinal joint system, continuous long lengths, vertical 25mm ribs and elegant defined lines. Each panel is secured with concealed clips and then each panel is crimped securely together with the use of special tools. The Standing Seam system requires two panel seams (male and female) to lap each other. This system was developed in Europe and has been used for 200 years as a way of complimenting contemporary architecture, making it an ideal solution for both contemporary and traditional designs. The Standing Seam system is one of the most versatile cladding systems available, whether it is for roofing or facades.
